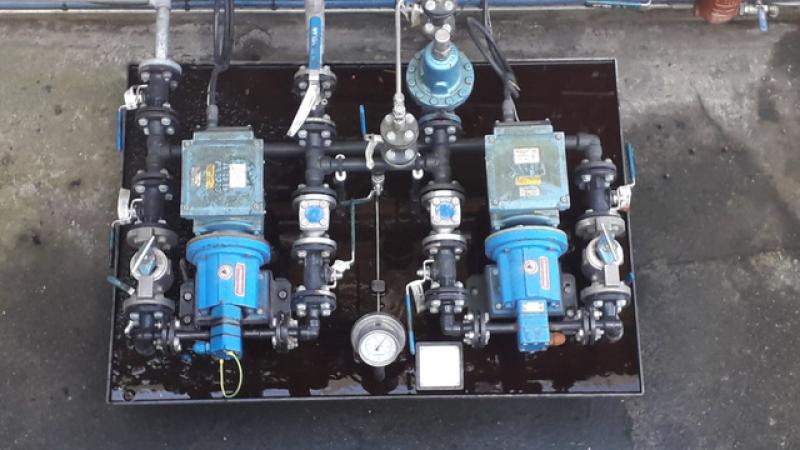
Fueling Reliability: How Viking Pump’s Mag Drive Solution Transformed Dye Injection for Ireland Fuel Distributor
09-02-2025
Discover how a fuel distributor in Ireland overcame pump reliability issues with Viking Pump’s SG805 Mag Drive solution—boosting efficiency, reducing maintenance, and ensuring compliance in a demandin...
See more
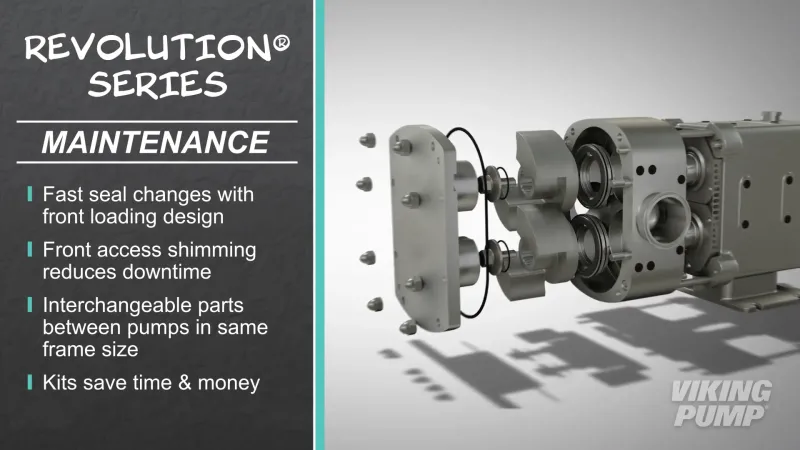
Revolution® Series Hygienic Pump Brings Flexibility to Difficult Applications
07-29-2025
Explore the customizable features of the Revolution® Series Pumps from Viking Pump, designed for efficiency and hygiene in various applications.
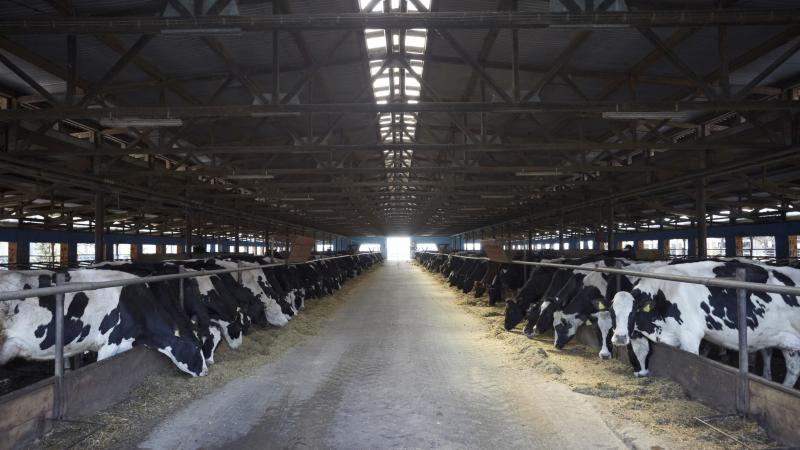
Efficient Molasses Pump Solutions
07-08-2025
Discover how Viking Pump's innovative pumps optimize the handling of viscous molasses for baking, animal feed, and industrial uses. Reliable, efficient, and designed for tough conditions.
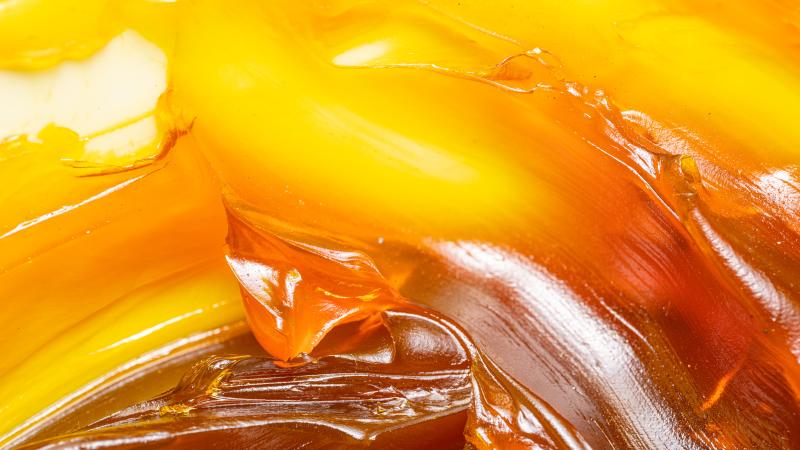
Grease Transfer Pumps: Solutions for Efficient Grease Handling
05-13-2025
Grease is an essential component in various industries, ensuring that machinery and equipment operate smoothly. A grease transfer pump plays a crucial role in the efficient handling of grease, whether...
See more
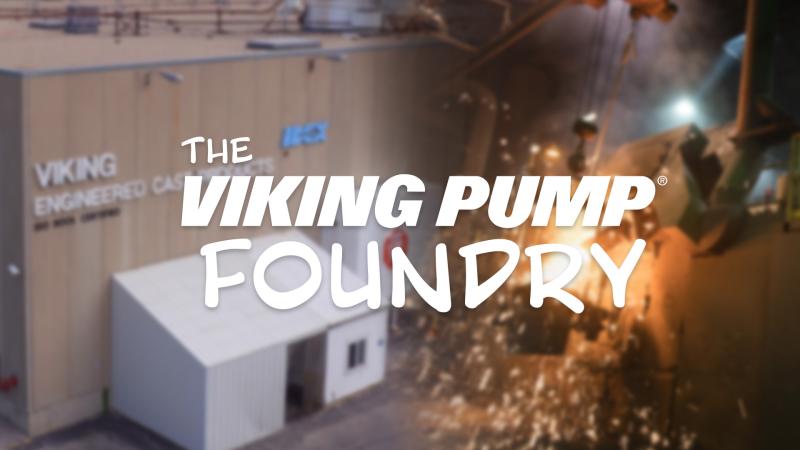
Exploring Viking Pump's Foundry: A Leader in Manufacturing Gear Pumps
04-14-2025
Welcome to the Viking Pump foundry in Cedar Falls, Iowa, where we’ve been at the forefront of manufacturing gear pumps for decades. Our foundry is a cornerstone of our vertical integration capabilitie...
See more
Robyn Watson
Sr. Marketing Coordinator
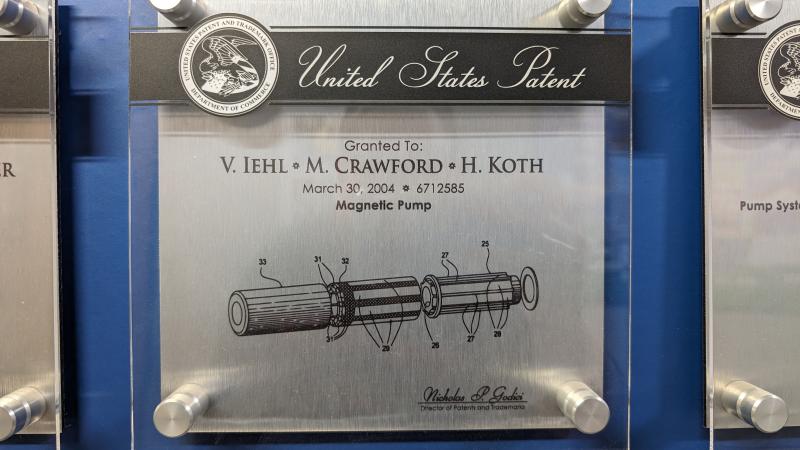
Universal Mag Drive, The Sealless Upgrade That Prevents Leakage and Fugitive Emissions
5 minutes
03-25-2025
Viking Pump invented, patented and manufactured the very first sealless mag drive rotary positive displacement (PD) pumps in the world, and developed several series over time for different application...
See more
John Hall
Pump Consultant
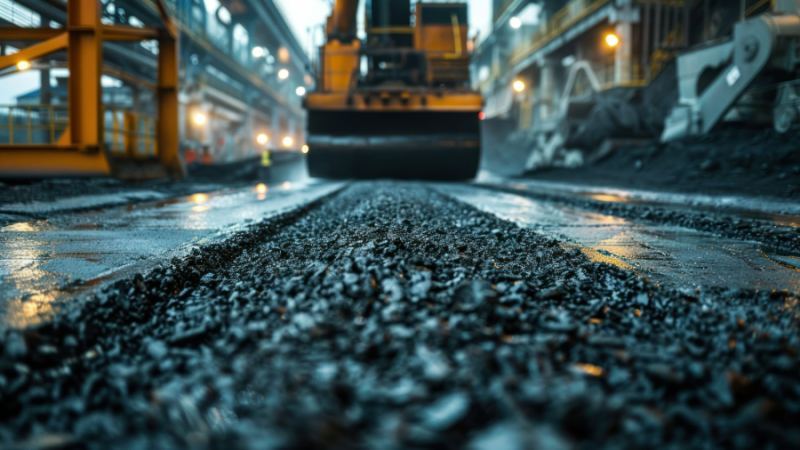
Bitumen vs Asphalt: Key Differences and Gear Pump Selection
02-25-2025
The terms bitumen and asphalt are often used interchangeably, but they are two completely different materials, causing confusion inside and outside the industry. Throw in regional differences in meani...
See more
John Hall
Pump Consultant
NPSH Visualized
02-11-2025
If you’ve ever fallen asleep reading pump texts about NPSH, you’re not alone. But here’s an easy-to-understand, graphical approach to ensuring your calculations.
John Hall
Pump Consultant
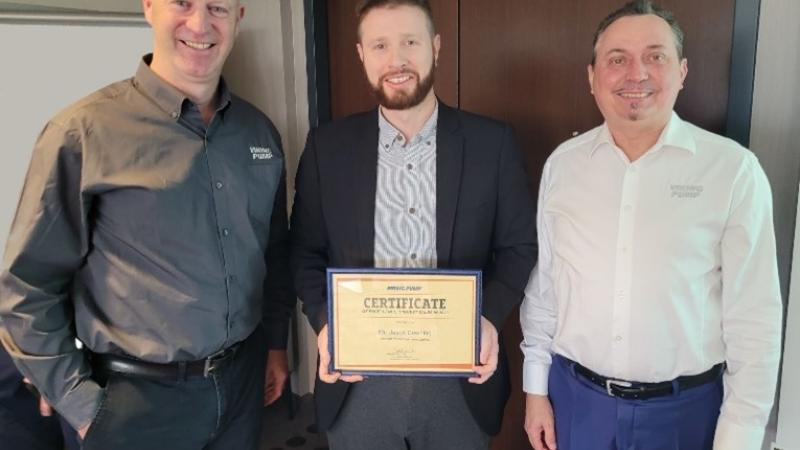
Distributor Spotlight | Michael Smith Engineers Ltd.
01-14-2025
Viking Pump is proud to have Michael Smith Engineers (MSE) as a distributor in Great Britain. The company has a solid reputation as one of the GB's leading pump specialists, providing solutions for di...
See more
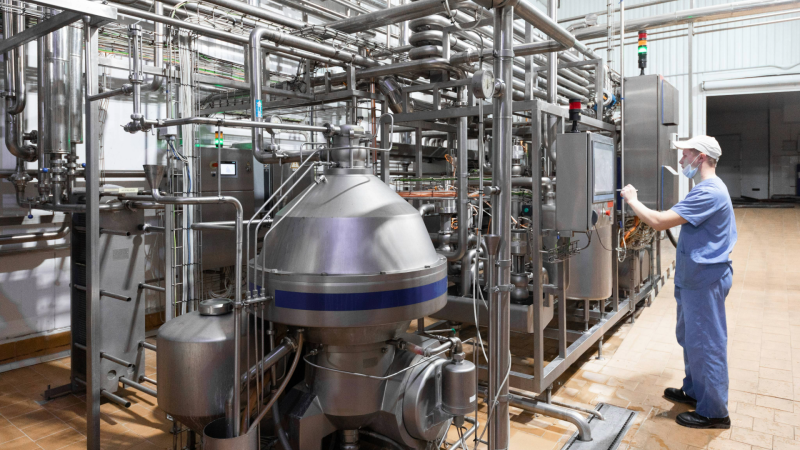
Four Ways to Source Hygienic Pumps
01-07-2025
There are really four main types of suppliers of hygienic, or sanitary pumps for food and pharmaceutical applications. There is no…