VIKING IN THE PROCESS:
Cast iron construction is generally adequate for most paint transfer pumps, but stainless steel may be necessary for certain water-based and latex varieties. Viking pumps deliver a steady and reliable flow rate, making them ideal for transporting key raw materials in paint production. These materials include resins, latex, solvents, oils, carriers, and additives. Paints also contain abrasive pigments, which differ based on color; common examples are titanium dioxide, iron oxide, and carbon black.
Paint and Coatings Applications
- Paint Manufacturing: The process of producing paints and coatings, where raw materials are mixed, pigments are dispersed, and solvents are added to create the final product. The manufacturing process requires precise mixing and uniformity to ensure quality and performance.
- Electrostatic Painting: A technique that utilizes electrical charges to attract paint particles to a surface. This method enhances the efficiency of the coating process, reduces waste, and provides a consistent and even finish, often used in automotive and industrial applications.
- Dip Tank Painting: In this process, objects are submerged into a tank filled with paint, ensuring complete coverage. It’s commonly employed for coating items with complex geometries or when a uniform coating is necessary for protection against corrosion.
- Curtain Coating: This method involves pouring a thin, continuous curtain of paint over a substrate as it passes through a coating chamber. It is ideal for flat surfaces, providing a smooth and even layer that is economical and efficient.
- Roller Coating: This technique uses a roller to apply paint evenly across a surface. Often used in industrial applications for coating large flat surfaces, it allows for speed and consistency.
- Paint Spraying: A popular application method where paint is atomized into a fine mist and sprayed onto a surface using a spray gun. Ideal for large areas and for achieving a smooth, high-quality finish, it is widely used in various industries including automotive and furniture manufacturing.
INDUSTRIAL PUMP RECOMMENDATIONS
4624B Series™ abrasive resistant pump
The 4624B Series™ internal gear pump was developed specifically to combat potential wear resulting from the handling of fine abrasives such as titanium dioxide, iron oxide, and carbon black. These pumps include an abrasive resistant seal, a tungsten carbide idler pin and bushing, and a seal support plan to flush particles away from the seal faces to extend pump life.
Features & Benefits
- Ultra-hard tungsten carbide idler pin and tungsten carbide idler bushing minimize wear in this key area, since a constant supply of abrasive material is flowing through the pumping elements.
- Behind-the-rotor pinned-seat mechanical seal with hard silicon carbide vs. silicon carbide seal faces, featuring external flush line from pump discharge to remove solids build-up, ensuring longest possible seal life (note: no flush line on F & FH sizes).
- The grease-lubricated bracket bushing is not contacted by the pumped liquid, for long life. The pump is re-greasable, with a lip seal at the stuffing box.
4624B Series™ Specifications
Pump Models | Standard Port Size | Nominal Pump Rating (GPM) | Nominal Pump Rating (m3/h) | Maximum RPM | Maximum Pressure PSI | Maximum Pressure BAR |
---|---|---|---|---|---|---|
F4624B | 0.5 | 0.75 | 0.17 | 870 | 100 | 7 |
FH4624B | 0.5 | 1.5 | 0.34 | 870 | 100 | 7 |
H4624B | 1.5 | 5 | 1.1 | 640 | 150 | 10 |
HL4624B | 1.5 | 10 | 2.3 | 640 | 150 | 10 |
K4624B | 2 | 25 | 5.6 | 280 | 150 | 10 |
KK4624B | 2 | 35 | 7.9 | 280 | 150 | 10 |
L4624B | 2 | 50 | 11.3 | 230 | 150 | 10 |
LQ4624B | 2.5 | 50 | 11.3 | 230 | 150 | 10 |
LL4624B | 3 | 65 | 14.8 | 230 | 150 | 10 |
LS4624B | 3 | 75 | 16 | 230 | 150 | 10 |
Q4624B | 3 | 110 | 25 | 190 | 125 | 9 |
QS4624B | 4 | 182 | 41 | 190 | 125 | 9 |
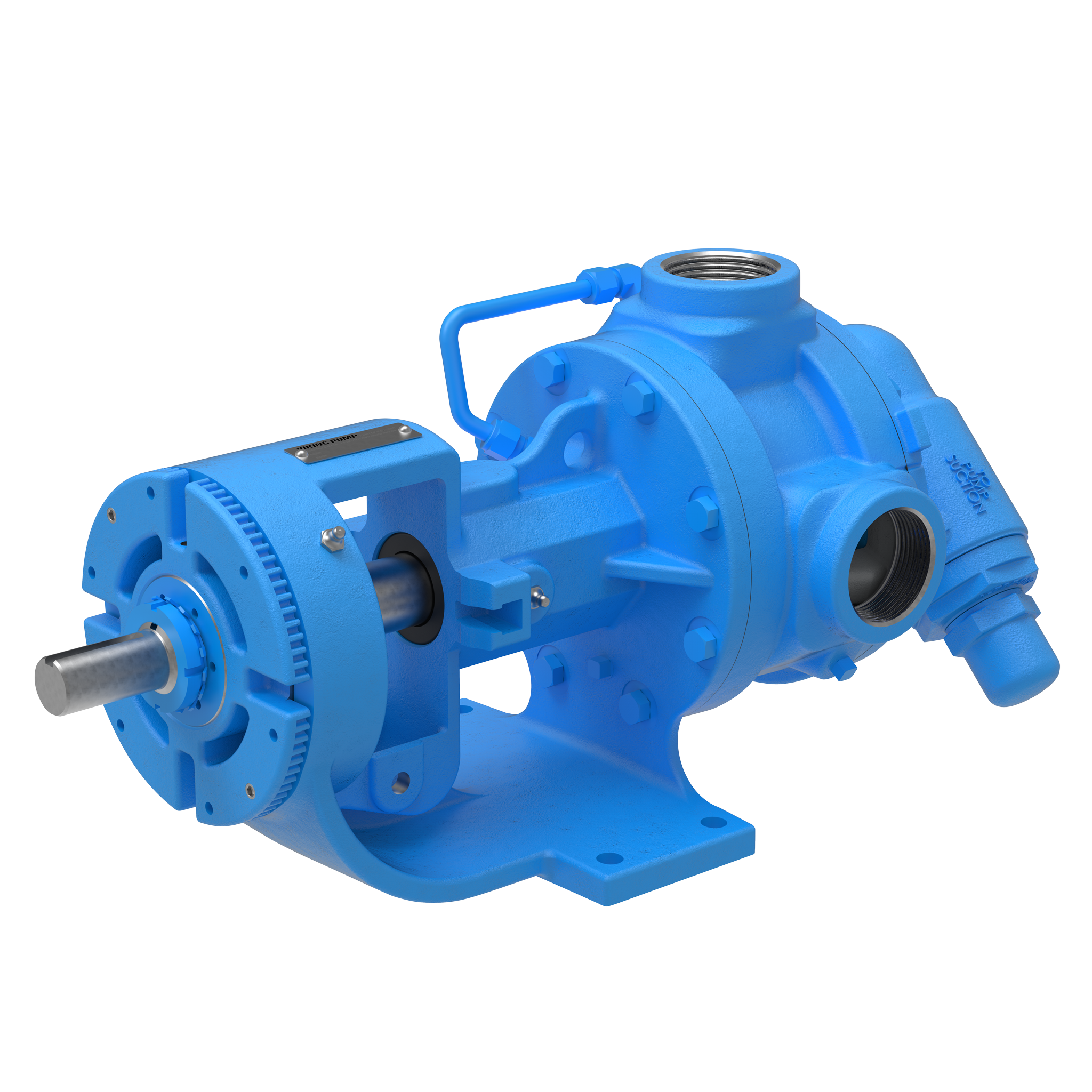
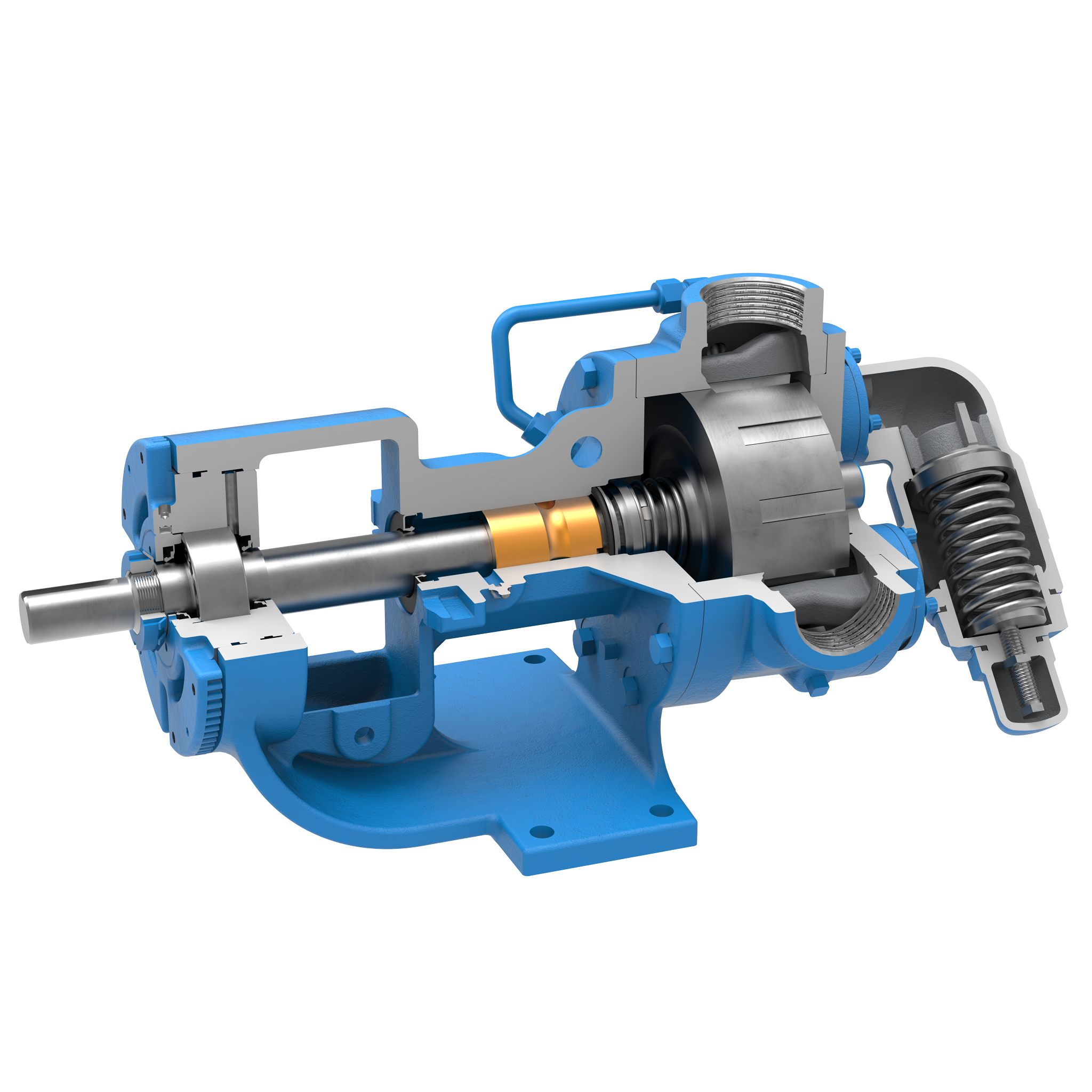
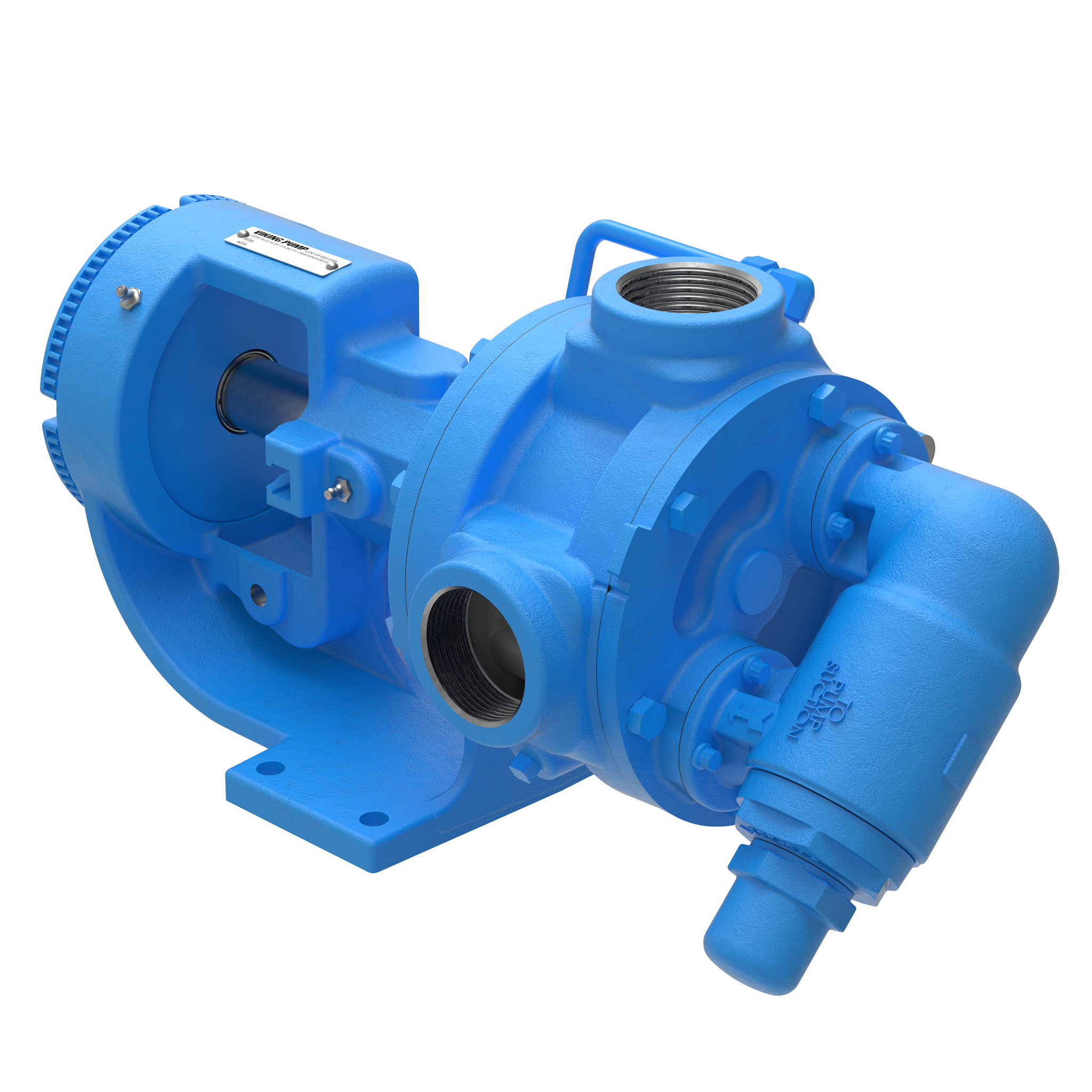
4127C Series™ internal gear stainless steel pump
The 4127C Series™ internal gear stainless steel paint pump is the flexible, simple, and adaptable solution for a wide range of applications. This new generation of pumps comes standard with the U-Plus™ bracket for mechanical seals, as well as the ProPort™ casing that accommodates a variety of port sizes and types depending on your needs. It can handle flow rates up to 320 GPM (73 m³/h).
Features & Benefits
- All stainless steel construction for corrosion resistance over a wider pH range
- ProPort™ casing utilizes mounting pads on each port designed to fit a variety of different flange types and sizes, enabling flexibility when connecting pumps to piping
- U-Plus™ bracket, available on H-QS sizes, offers seal location to be in the stuffing box or behind the rotor
- Opposite porting on all pump sizes available
4127C SERIES™ SPECIFICATIONS
Pump Models | Standard Port Size | Nominal Pump Rating (GPM) | Nominal Pump Rating (m3/h) | Maximum RPM | Maximum Pressure PSI | Maximum Pressure BAR |
---|---|---|---|---|---|---|
H4127C | 1.5 | 10 | 1.9 | 1150 | 150 | 10 |
HL4127C | 1.5 | 20 | 3.7 | 1150 | 150 | 10 |
K4127C | 2 | 50 | 11 | 520 | 150 | 10 |
KK4127C | 2 | 65 | 15 | 520 | 150 | 10 |
L4127C | 2.5 | 100 | 23 | 520 | 150 | 10 |
LL4127C | 3 | 135 | 31 | 520 | 150 | 10 |
LS4127C | 3 | 160 | 36 | 520 | 150 | 10 |
Q4127C | 4 | 200 | 45 | 350 | 150 | 10 |
QS4127C | 6 | 320 | 73 | 350 | 150 | 10 |
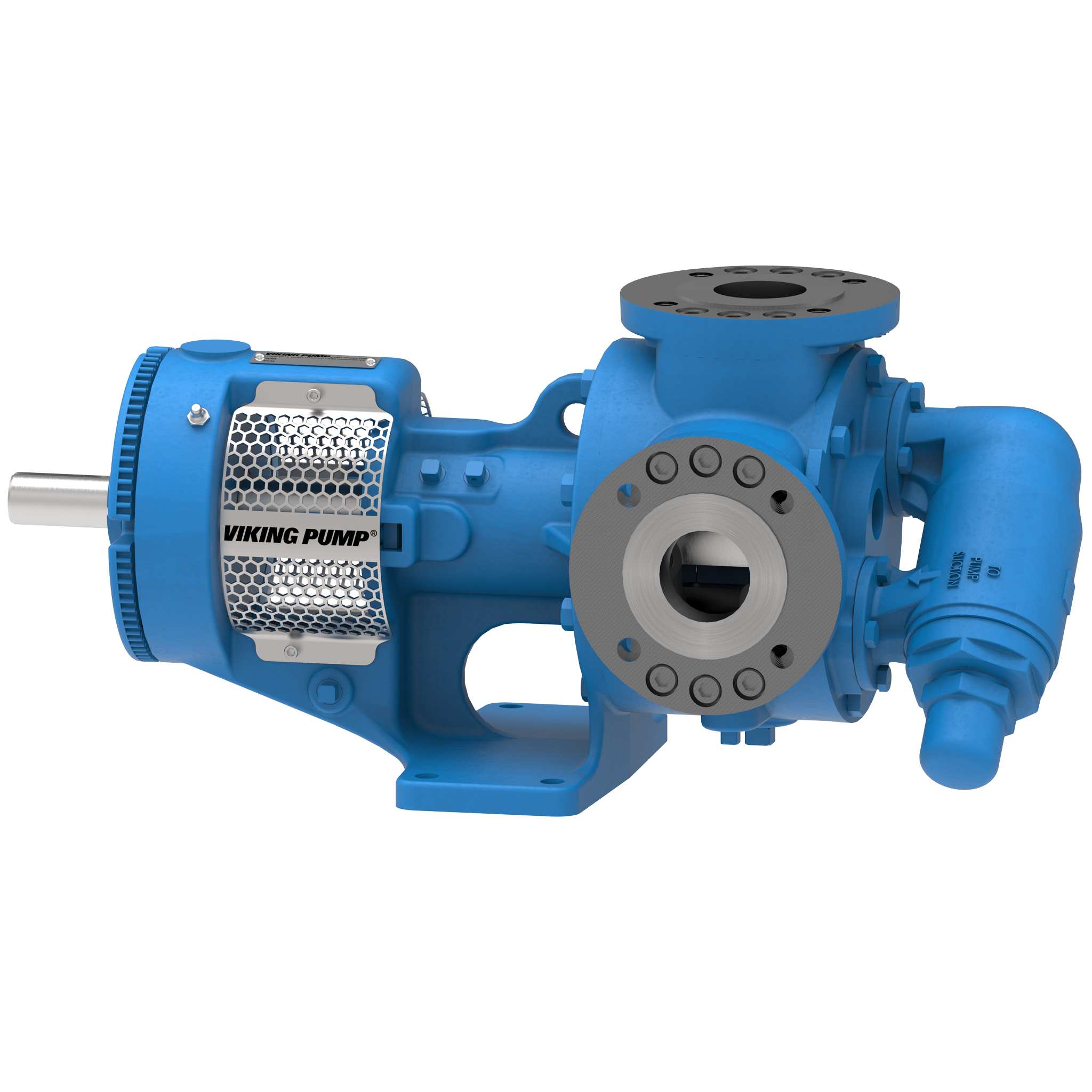
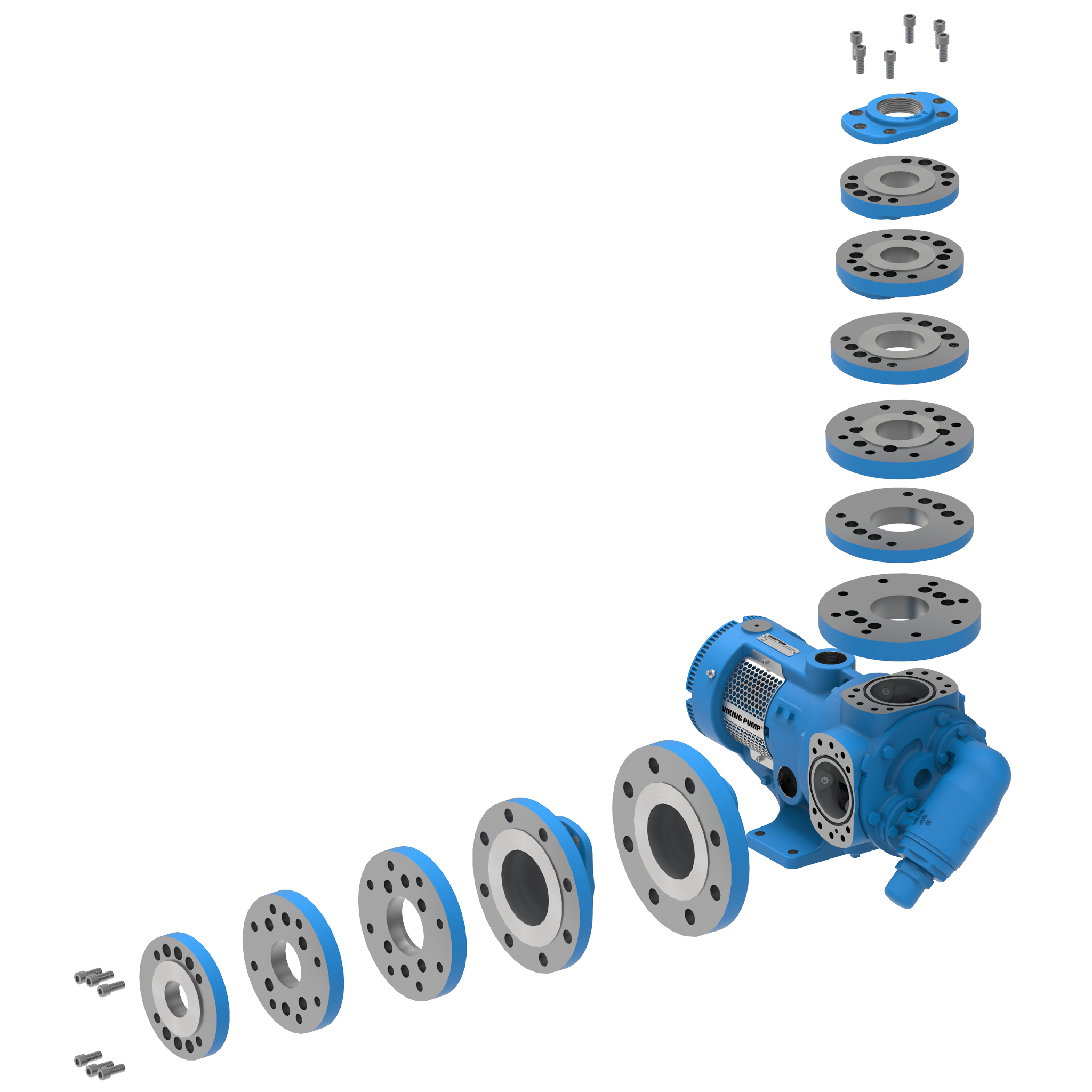
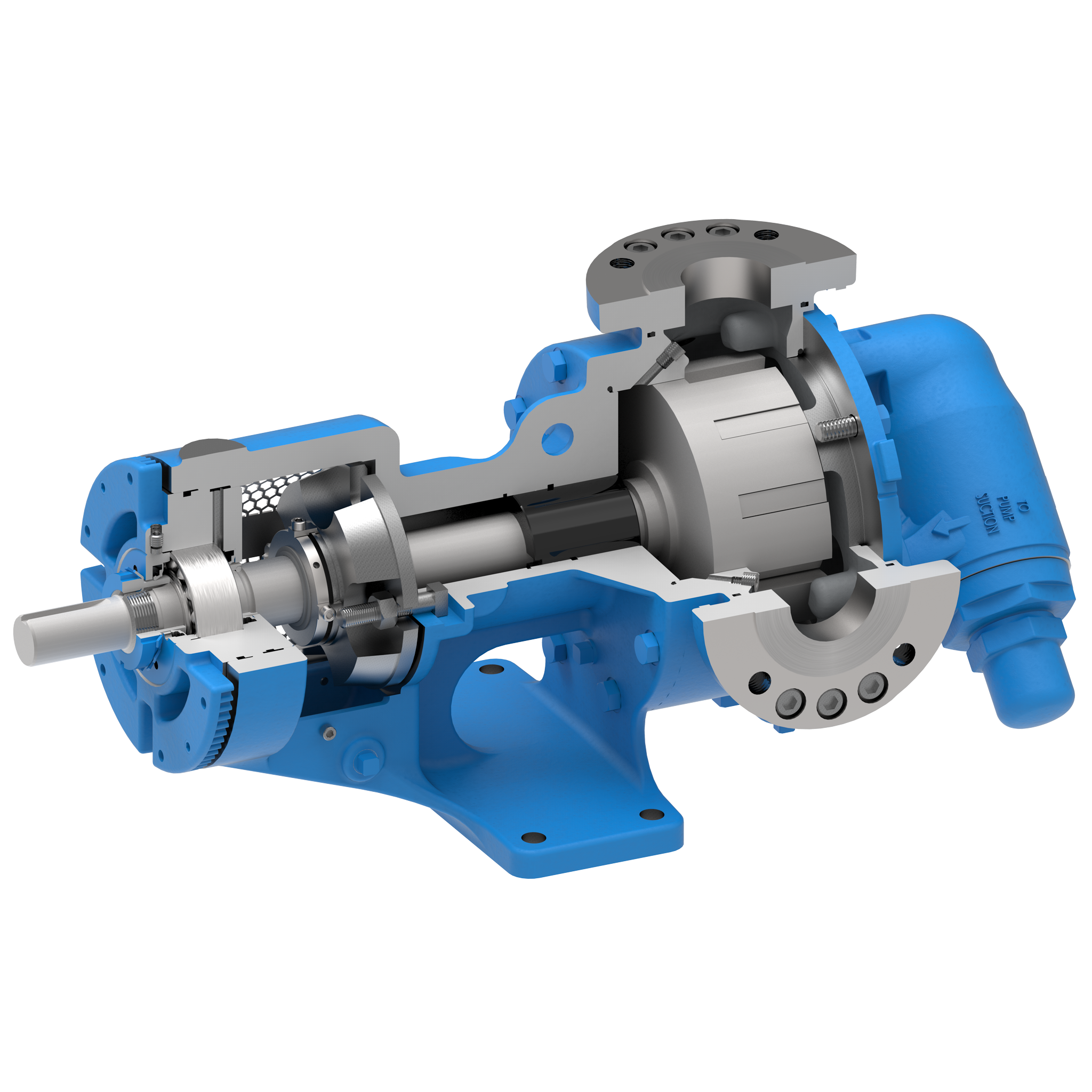
1124A Series™ cast iron gear pump
The 1124A Series™ internal gear pump with O-Pro® Seal technology is the perfect solution for adhesives, starch, polymers, and more due to it's reliable sealing as well as easy maintenance. It can handle flows from 8 to 400 GPM (1.8 to 91 m³/h).
Features & Benefits
- Rugged design provides superior performance in many markets
- Tight clearances offer high efficiency and excellent priming capabilities
- O-Pro® Barrier combines reliable sealing with easy maintenance
- O-Pro® Barrier is standard with FKM elastomers
1124A SERIES SPECIFICATIONS
Pump Models | Standard Port Size | Nominal Pump Rating (GPM) | Nominal Pump Rating (m3/h) | Maximum RPM | Maximum Pressure PSI | Maximum Pressure BAR |
---|---|---|---|---|---|---|
H1124A | 1.5 | 8 | 1.8 | 1000 | 200 | 14 |
HL1124A | 1.5 | 18 | 4 | 1000 | 200 | 14 |
K1124A | 2 | 80 | 18 | 780 | 200 | 14 |
KK1124A | 2 | 100 | 23 | 780 | 200 | 14 |
LQ1124A | 2 | 135 | 31 | 640 | 200 | 14 |
LQ1124A | 2.5 | 135 | 31 | 640 | 200 | 14 |
LL1124A | 3 | 140 | 32 | 520 | 200 | 14 |
LS1124A | 3 | 200 | 45 | 640 | 200 | 14 |
Q1124A | 4 | 275 | 62 | 470 | 200 | 14 |
QS1124A | 6 | 400 | 91 | 470 | 200 | 14 |

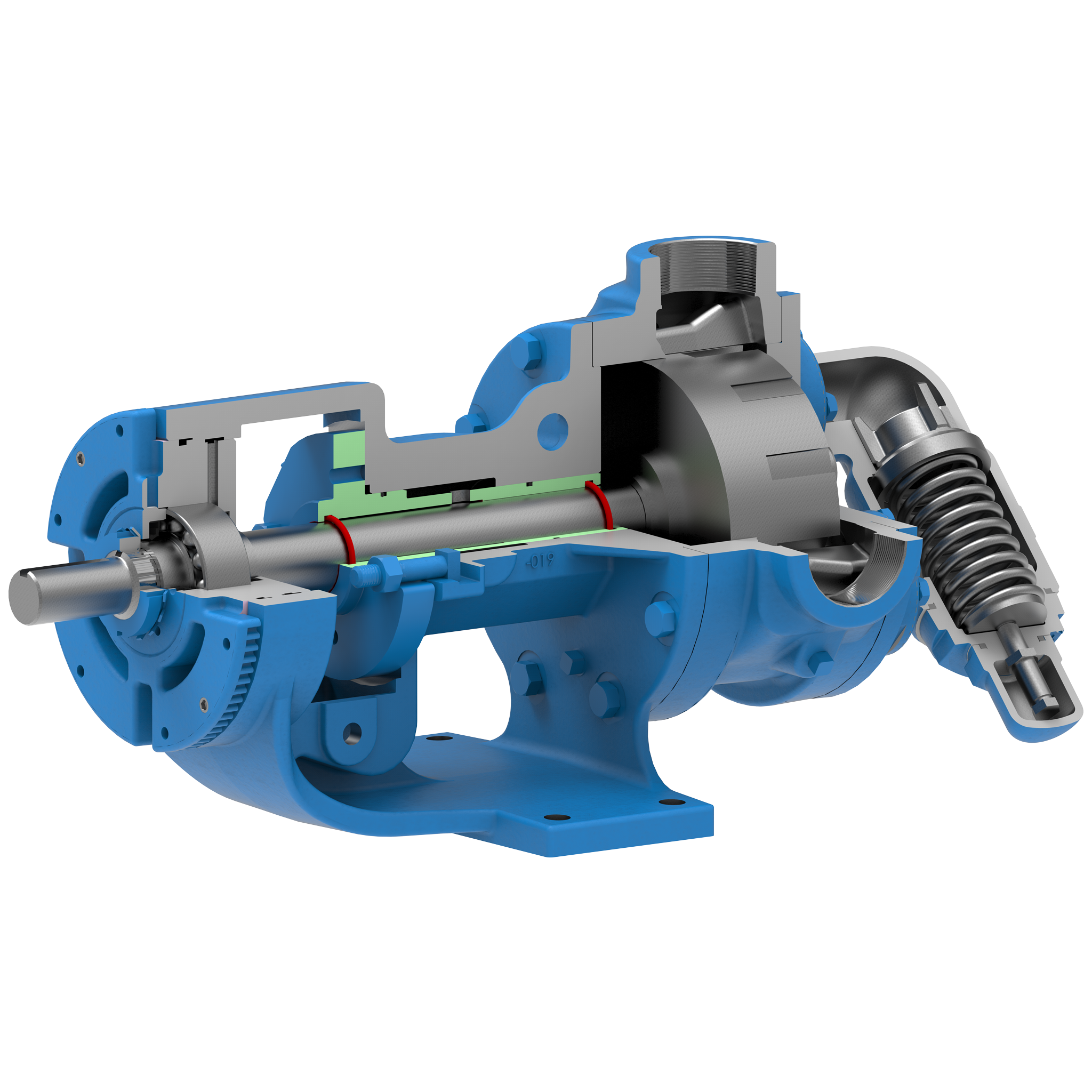
Viking's internal gear positive displacement pumps are ideal for manufacturing paints & coatings for several key reasons:
- Smooth and Consistent Flow: Internal gear pumps provide a smooth, continuous flow without pulsations, which is crucial in paint manufacturing to ensure uniformity in the final product.
- Handling a Wide Range of Viscosities: Paint ingredients can range from being very thin to almost a solid, and internal gear pumps are well-suited to handle this wide range effectively. Clearances can be dialed in to suite the specific liquid without compromising on efficiency or performance.
- Precision and Control: These pumps offer precise control over the flow rate, which is essential for ensuring accurate mixing and consistency in paint formulations.
- Self-Priming and Suction Capabilities: Internal gear pumps are capable of self-priming and produce strong suction. This feature is beneficial in the paint manufacturing process for drawing paint from storage tanks and mixing tanks with ease.
- Durability and Versatility: Constructed from robust materials in our very own foundry located in Cedar Falls, Iowa, our internal gear pumps can handle abrasive and corrosive components often found in paints. Their durability makes them suitable for the demanding environment of paint production.
- Low Maintenance: They generally have fewer moving parts and are designed for long-term operation with minimal maintenance, reducing downtime and increasing efficiency in the production line.
- Gentle Handling of Fluids: The design of internal gear pumps ensures gentle handling of fluids, which helps in maintaining the integrity of the paint's components and preventing the shear-sensitive materials from degrading.
Overall, the combination of these attributes makes internal gear pumps a reliable and efficient choice for fluid transfer in paint manufacturing operations, ensuring high-quality and consistent outputs.
Contact Us
With over 110 years of experience providing positive displacement pumping solutions, Viking Pump has a rich, lengthy history of providing engineered solutions for tough applications. We have dedicated sales and field support specialists who are supported by a team of customer service representatives and engineers. Our knowledgeable team of application engineers available to help with product selection and technical support. USA based company with vertically integrated manufacturing facility.
ALL PUMPS FACTORY TESTED
Our state-of-the-art testing equipment is used to confirm performance prior to shipments. Our world-class lab gives Viking Pump the ability to test our pump designs across a range of relevant variables.
TEST LAB
Our world-class lab gives Viking the ability to test its glycol pump designs across a range of relevant variables.
VERTICALLY INTEGRATED PRODUCTION PROCESS
Viking Pump operates a foundry, a 200,000+ sq. ft. machining, assembly and testing center, and an extensive product engineering and testing lab in its world headquarters in Cedar Falls, Iowa, USA. This level of vertical integration ensures maximum quality, ability to satisfy special needs, and to meet project schedules.