The GB-410 Series™ external gear pump is the ultimate durable, reliable, field-rebuildable solution for your high-pressure oil and gas processing needs. With its hardened parts for enhanced wear resistance, it was engineered specifically for overcoming the challenges of upstream and midstream oil and gas processing applications such as natural gas & CO2 dehydration (glycol), LACT – pipeline injection, gas sweetening (amines), pigging, and condensate transfer.
- High temperature rating
- Robust durable pump design
- Rebuildable design
- Reliable mechanical seal solutions
- Easy field installation
- Flow rates up to 67 GPM
- Operating Pressure up to 1500 PSI
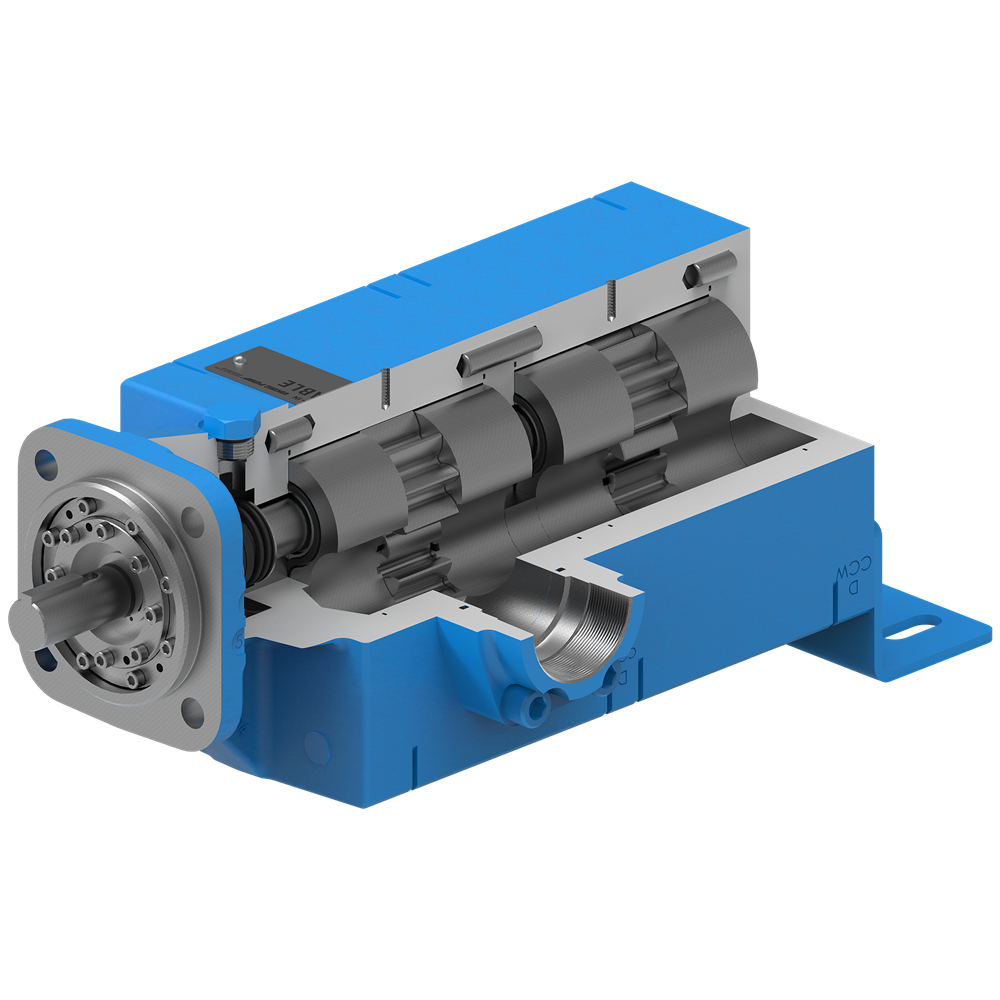
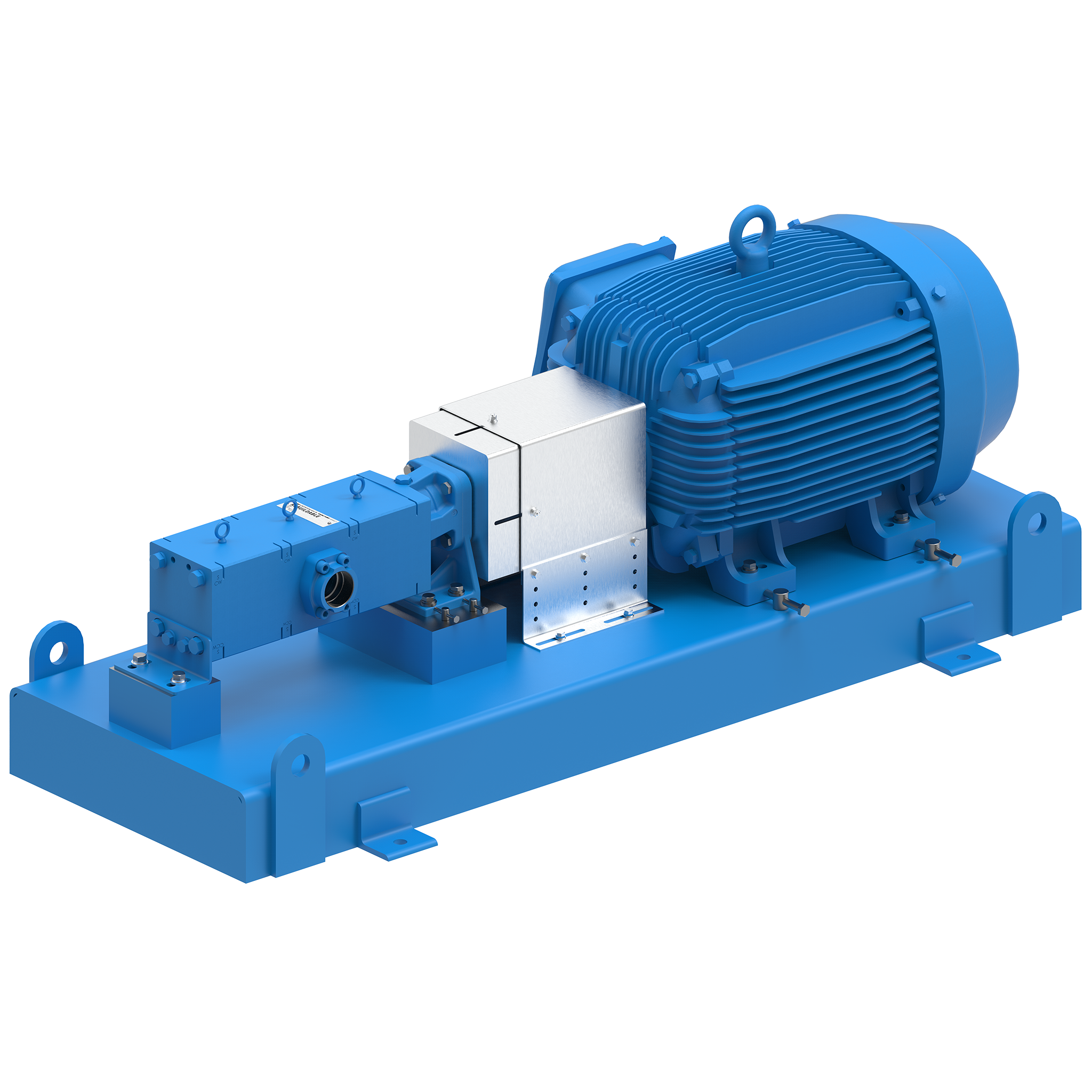
Through this process, we understand the struggle:
- Thermal shock at start up
- Low viscosity product
- High pressure differential
- Abrasives causing quick wear and tear
- 24/7 operation in high temp, low lubricity conditions
Multiple Sealing Options
- Single cartridge mechanical seal standard
- Double and tandem cartridge mechanical seals available
- Capable of accepting an API 682 seal
Durable Construction
- Heat treated shaft and spur gears provide reliable service
- Internal surfaces are Vitek hardened to increase wear resistance
Modular Port Design
- 6", 180° 4 bolt ports standard
- Weldneck port adapter design allows for multiple interchangeable flange options
- Direct drive, motor-speed operation eliminates the need for gearboxes or belt drives
- Standard inverter duty rated motors
Reduced Maintenance
- Back pull-out seal design and spacer coupling eliminate the need to disturb piping or perform alignments during seal changes
- Rigid structural steel base with milled mounting pads and jacking bolts for ease of field alignment
- No pulsation dampeners, gear reducers, belt drives, or additional equipment to service and maintain
With over 110 years of experience providing positive displacement pumping solutions, Viking Pump has a rich, lengthy history of providing engineered solutions for tough applications. We have dedicated sales and field support specialists who are supported by a team of customer service representatives and engineers. Our knowledgeable team of application engineers available to help with product selection and technical support. USA based company with vertically integrated manufacturing facility.
ALL PUMPS FACTORY TESTED
Our state-of-the-art testing equipment is used to confirm performance prior to shipments. Our world-class lab gives Viking Pump the ability to test our pump designs across a range of relevant variables.
TEST LAB
Our world-class lab gives Viking the ability to test its glycol pump designs across a range of relevant variables.
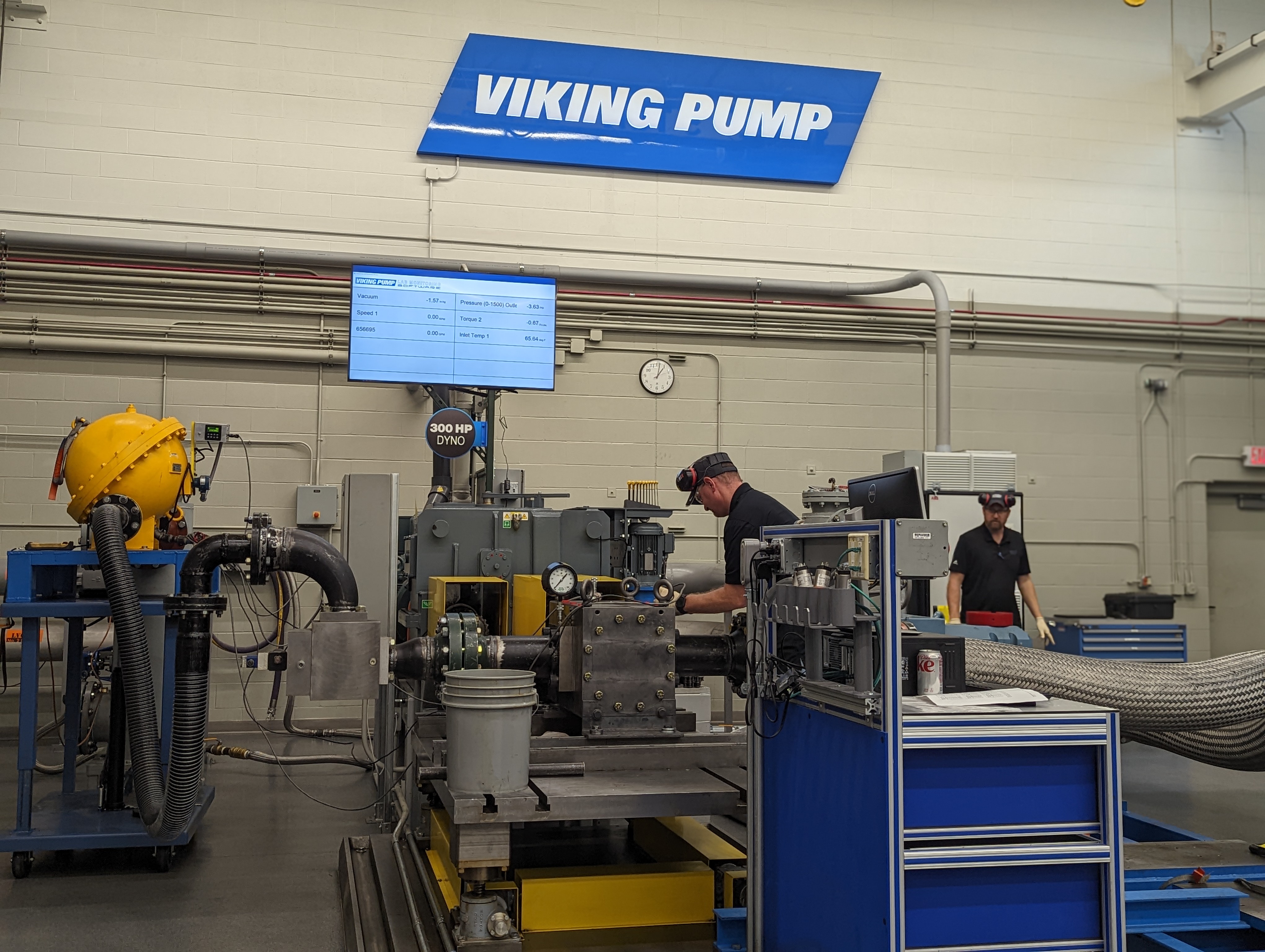
Related Articles
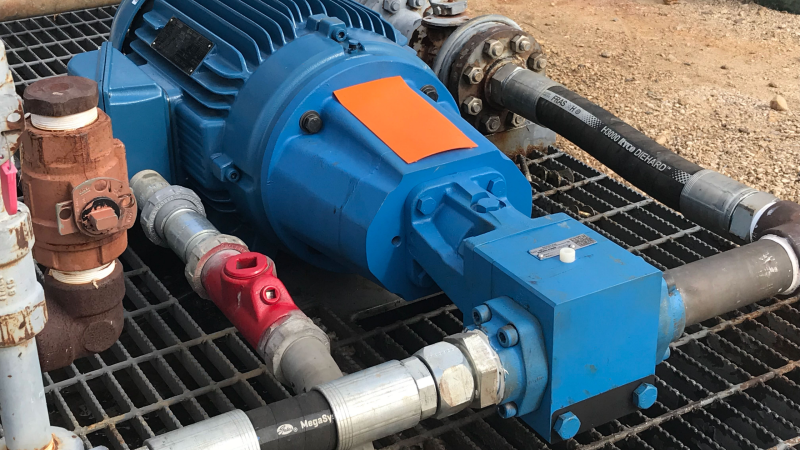
Driving Natural Gas with Glycol Pumps
Industrial gear pumps have many uses in a wide array of market applications—ranging from food processing to pouring asphalt. A growing area in need of specialized gear pumps is in the oil and gas industry, particularly with regards to the removal of water from natural gas via dehydration. Viking Pump entered this market to support customers striving to deliver high-quality product 24/7 to their end users in the face of rising global natural gas consumption. This increasing demand is expected to continue through 2040, due to population growth, coal displacement by cleaner energy, fracking, etc.
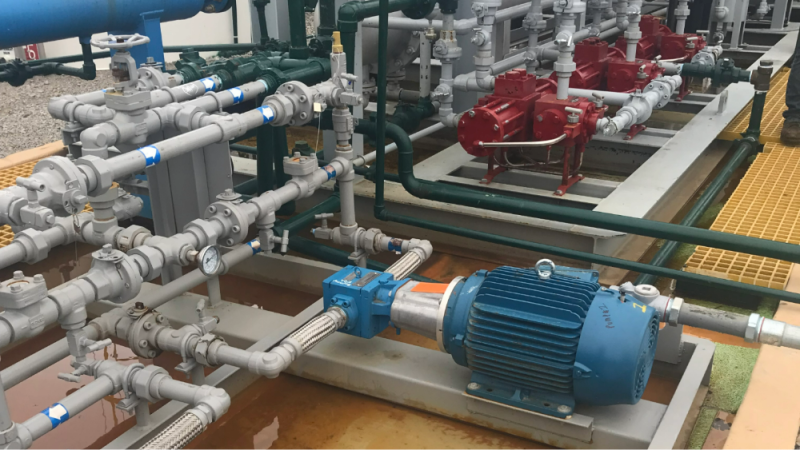
U.S. EPA Bans Natural Gas-Driven Pumps
A new EPA rule, published December 2, 2023, covering new and existing oil and gas operations, requires the use of zero-emissions pumps instead of natural gas-driven pumps, with very few exceptions. It also restricts other natural gas-driven equipment, limits fugitive emissions and calls for reduced flaring of associated gas
Natural gas dehydration is a process used in the removal of water vapor- or water content- in natural gas so that it meets pipeline quality standards. It's important because high levels of water vapor in the natural gas can cause corrosion and freezing, resulting in costly repairs. But what exactly is natural gas dehydration? Here's everything you need to know about this important process:
The Gas Dehydration process
The process of natural gas dehydration generally consists of two steps. The first involves adding glycol to the natural gas in order to absorb any additional water vapor present in it. Glycol has a molecular structure that reacts with water molecules, allowing it to lower the dew point temperature of the natural gas.
The second step involves running the glycol-treated natural gas through a regeneration tower, which removes all traces of absorbed water molecules from the glycol. This results in “dry” natural gas meeting pipeline quality standards for moisture content at temperatures below the dew point.
Benefits of Natural Gas Dehydration Process
Using an efficient and effective dehydration system will help ensure that pipelines remain undamaged and operational for an extended period of time. Additionally, dehydration promotes safety as moisture can create pockets within pipes where flammable gases may accumulate and cause fires or explosions when ignited by heat from nearby machinery or other heat sources. By dehydrating pipelines regularly, companies can avoid costly repair bills due to pipe corrosion caused by elevated moisture levels in their pipes and facilities.
The natural gas dehydration process is a critical process in the production and distribution of gas resources across various industries today. By decreasing humidity levels down to acceptable rates through efficient technology such as absorption systems and adsorption systems, it is easy to maintain clean lines and extend the life span of pipeline systems while promoting safe working conditions for employees operating these networks on behalf of their companies or organizations.
What our customers are saying
"Viking's engineering team listened to us and was willing to keep trying different things in order to make a pump that can handle the challenges of glycol dehydration... Switching to Viking has been a great success all around. The customers are happy and so are we!"
-Jerry, Service manager, Marcellus Shale
"Viking has the best customer service I have experienced in the industry. The pumps have performed flawlessly, far better than similar setups. Quick and easy conversion and setup."
-Justin, Facilities technician Sr., Utica Shale